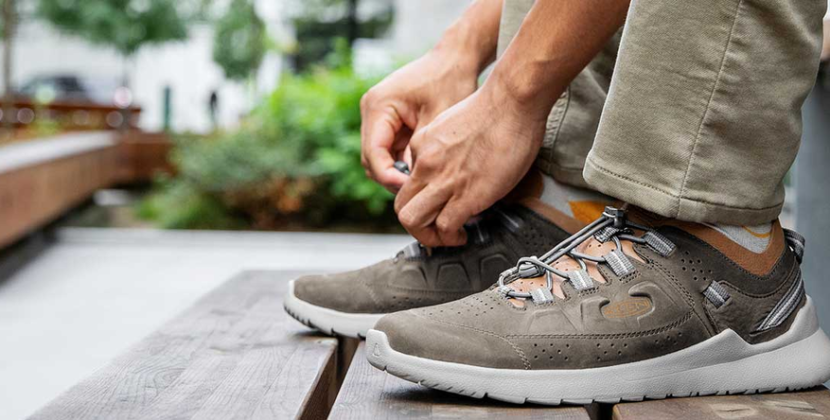
In the ever-evolving world of aerospace and defense, innovation is essential for staying competitive and meeting the stringent demands of the industry. One such innovation that has been transformative is 3D printing, also known as additive manufacturing (AM). This technology has rapidly grown in popularity due to its ability to produce complex geometries, lightweight components, and reduce costs. In this article, we’ll explore the benefits of 3D printing for aerospace and defense, with examples of its application in both industries.
1. Low-Volume Production with 3D Printing
Aerospace and defense industries are often focused on producing highly complex parts in limited quantities. This makes low-volume production an ideal scenario for 3D printing. Traditional manufacturing methods require expensive tooling and setup costs, which aren’t cost-effective for producing small batches of parts. However, 3D printing allows for cost-effective, rapid production of components without the need for dedicated tooling.
For example, aerospace OEMs (original equipment manufacturers) and suppliers can create small batches of customized parts, such as turbine blades or engine components, without significant upfront investment. By 3D printing lightweight parts, companies also benefit from reduced lead times, leading to more flexible production processes.
Benefit: The ability to produce complex, low-volume parts at a reduced cost.
2. Weight Reduction in Aircraft Design
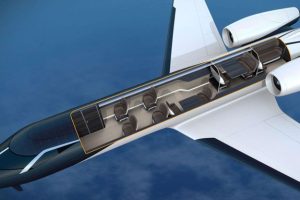
Weight reduction is a crucial aspect of aircraft design, as even a small reduction in weight can lead to significant savings in fuel consumption and a reduction in carbon dioxide emissions. This is particularly important as the aerospace industry aims to reduce its environmental footprint.
3D printing enables manufacturers to produce lightweight parts using materials that offer both strength and reduced mass. Generative design software can be integrated into the design process to optimize part geometry, further improving the efficiency of these lightweight components. This is especially useful in producing aircraft interiors, such as spacer panels and wall components, which need to be light yet durable.
For example, Airbus uses 3D printing to create 15% lighter spacer panels for its A320 aircraft, contributing to overall fuel savings and reduced emissions.
Benefit: Lightweight parts created via 3D printing contribute to fuel efficiency and reduced emissions.
3. Material Efficiency
Traditional manufacturing methods, such as machining, involve cutting away excess material, leading to significant waste. In contrast, 3D printing builds parts layer by layer, meaning material is used only where it is needed. This process results in significantly less waste, which is particularly important when working with expensive materials like high-performance alloys or titanium used in aerospace applications.
In addition to the reduced waste, 3D printing also offers material efficiency through its expanding range of printable materials. These materials include thermoplastics like ULTEM 9085 and metals such as aluminum, titanium, and nickel-based alloys, all of which are crucial for creating high-performance aerospace components.
Benefit: Less waste during production, leading to cost savings and more efficient material usage.
4. Part Consolidation for Simplified Assembly
Part consolidation is one of the most exciting opportunities provided by 3D printing in the aerospace and defense sectors. Instead of manufacturing and assembling multiple individual components, 3D printing allows engineers to create single, consolidated parts. This simplification reduces the number of parts needed, leading to easier assembly, faster maintenance, and less time spent on quality control.
A prominent example is ArianeGroup’s development of a 3D-printed injector head for the Ariane 6 launcher. Traditionally, the injector head was made up of 248 individual parts, which needed to be machined and welded together. With 3D printing, these components were reduced to a single piece, saving time and money in both production and maintenance.
Benefit: Reduced assembly complexity and faster maintenance due to part consolidation.
5. Maintenance and Repair with Metal 3D Printing
Aircraft have long lifespans, often ranging between 20 to 30 years, meaning maintenance, repair, and overhaul (MRO) services are critical in ensuring their operational efficiency. Metal 3D printing technologies, such as Direct Energy Deposition (DED), offer innovative solutions for repairing aerospace and defense equipment.
One of the main advantages of metal 3D printing is that worn-out components, such as turbine blades, can be repaired by adding material only to the worn areas. This is not only faster but also less expensive than producing an entirely new part. For military applications, this ability to repair high-end equipment, such as jet engine components, ensures that defense operations run smoothly without long downtimes.
Benefit: Quicker, more cost-effective repairs that extend the lifespan of critical components.
6. Tooling Production with 3D Printing
In aerospace manufacturing, the need for specialized tooling such as jigs and fixtures is essential. Traditionally, producing custom tooling involved lengthy processes, often taking weeks to manufacture. However, 3D printing can reduce these lead times dramatically.
For example, Latécoère, a French aerospace manufacturer, uses 3D printing to create custom tooling in just a few days—a 95% reduction in lead times compared to traditional methods. This approach also saves costs, as 3D-printed tools are around 40% cheaper than those produced using CNC machining.
Similarly, Moog Aircraft Group uses FDM 3D printing to produce tools like coordinate measuring machines (CMMs) in-house. By bringing the process in-house, the company cut production times from six weeks to 20 hours, with significant cost savings.
Benefit: Faster and more cost-effective production of custom tooling.
7. Spare Parts Production
In aerospace and defense, spare parts are often needed urgently to keep operations running. Traditionally, manufacturers relied on large inventories of spare parts, but 3D printing is transforming the spare parts supply chain by allowing companies to print parts on demand. This reduces inventory costs and ensures that parts can be produced quickly when needed.
For example, Satair, an Airbus subsidiary, uses additive manufacturing to produce plastic and metal spare parts. This allows the company to meet the urgent demands of aircraft maintenance, reducing lead times and improving the overall efficiency of the supply chain.
Benefit: Quicker production of spare parts, reducing inventory costs and supply chain complexities.
8. Aerospace Applications of 3D Printing
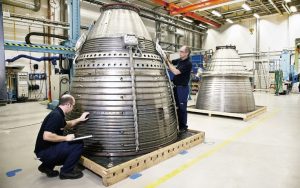
3D printing has a wide range of applications in aerospace, from producing rocket components to creating aircraft interiors. The technology has enabled companies like Airbus and Boeing to push the boundaries of what’s possible in aircraft design and manufacture.
For example, ArianeGroup has successfully 3D-printed components for its rockets, significantly reducing production times and costs. In the case of aircraft interiors, Airbus has produced lightweight, customized panels for its commercial aircraft, enhancing both performance and aesthetic appeal.
Benefit: Innovative designs and reduced production times for aerospace components.
9. Defense Applications of 3D Printing
The defense industry has also embraced 3D printing for producing complex parts such as drone components, antennas, and engine brackets. The flexibility of 3D printing allows for rapid prototyping and the ability to quickly produce small batches of military equipment.
One notable example is the collaboration between Harris Corporation and Nano Dimension, which used electronics 3D printing to create antennas. By producing these antennas in-house, the companies were able to accelerate the product development process and reduce reliance on third-party suppliers.
Benefit: Accelerated product development and reduced costs in defense applications.
Conclusion
The aerospace and defense industries are continually seeking ways to improve efficiency, reduce costs, and increase performance. 3D printing offers numerous benefits, from low-volume production and weight reduction to material efficiency and part consolidation. With its ability to create lightweight components, improve maintenance and repair processes, and reduce tooling lead times, 3D printing is transforming the way these industries operate. As more companies invest in the technology, the future of 3D printing in aerospace and defense looks incredibly promising, opening doors to new possibilities for innovation and growth.