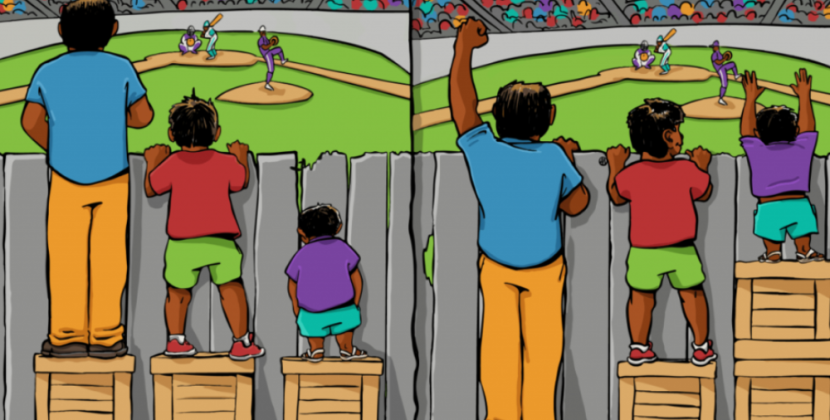
The car manufacturing industry has been around for over a century, and while it has undergone significant changes throughout the years, there’s one aspect that remains relatively unchanged: the production process. That is until now. A new tool has emerged in the industry that promises to change everything we know about car manufacturing. In this blog post, we’ll take a deep dive into this groundbreaking technology and uncover how it’s revolutionizing the game as we know it. Buckle up and get ready to discover the hidden truths of car manufacturing!
The current state of the car industry
The car industry has come a long way since its inception, and today it’s one of the most vital sectors in the global economy. The industry contributes billions to national economies and provides millions of jobs worldwide.
With advancements in technology, we’ve seen changes in the type of cars being produced. Electric vehicles (EVs) are becoming increasingly popular as more people become aware of their environmental benefits. In fact, some countries have pledged to ban petrol-powered cars altogether by 2030.
The automobile sector has also been impacted by COVID-19 with many factories shutting down due to concerns over worker safety. This led to a significant drop in production levels globally and resulted in job losses across multiple companies.
However, despite these challenges, the demand for cars remains strong. As we move towards a future that is increasingly digitized and environmentally conscious, there’s no doubt that innovation will continue driving change within this dynamic industry.
The new tool that’s shaking things up
The car manufacturing industry has always been known for its complex and intricate processes. However, with the advancement of technology, a new tool has emerged that is changing the game. This tool is called Augmented Reality (AR) and it’s shaking things up in ways never seen before.
AR allows car manufacturers to visualize their designs in 3D models, providing them with a more accurate representation of how their products will look like once they are manufactured. With this new technology, manufacturers can easily identify design flaws and make necessary changes before production even begins.
AR also offers an immersive experience for customers who can now use mobile devices to view detailed 3D models of cars from different angles right from the comfort of their homes. Customers can customize color options and add-ons without having to visit dealerships physically saving them time and effort.
The benefits of AR extend beyond just design and customer experience improvements but also include cost-saving advantages as well as reducing production errors while improving efficiency which saves time during assembly lines operations.
However, despite all these benefits there could be potential downsides such as privacy concerns if personal data collected by AR used without user consent or ethical issues surrounding counterfeit parts being produced using this technology.
All in all, AR is proving to be one revolutionary tool that’s transforming how car manufacturing operates.
How this tool is changing the game
The tool that is changing the game in car manufacturing is none other than 3D printing. With this technology, manufacturers can now create parts and components for their vehicles faster and more efficiently than ever before. This means lower costs, faster production times, and ultimately better quality cars for consumers.
Traditionally, car parts have been made using molds or casts which are expensive to produce and take a long time to make. But with 3D printing, all you need is a digital file of the part you want to create, and the printer does the rest. This reduces lead times significantly.
Another advantage of 3D printing is that it allows for greater customization of car components. Manufacturers can easily tweak designs on a computer before sending them to be printed out in real life. This means they can cater more specifically to different markets or even individual customers.
Perhaps one of the most exciting aspects of 3D printing in car manufacturing is its potential impact on sustainability. By reducing waste from traditional casting methods and using recycled materials like plastic bottles as feedstock for printing filament, we could see significant reductions in environmental impact across the industry.
There’s no doubt that 3D printing has become an indispensable tool for modern-day vehicle manufacturers looking to stay ahead of competitors while also delivering high-quality products at reasonable prices.
The benefits of this new tool
The new tool in car manufacturing is revolutionizing the industry by providing several benefits to automakers. One of the most significant advantages of this tool is that it reduces waste, which helps manufacturers save money and minimize their environmental footprint.
By using real-time data to monitor production processes, this tool can identify areas where materials are being wasted or used inefficiently. This allows manufacturers to make adjustments on the fly and reduce their overall waste output.
Another benefit of this new tool is that it improves product quality. By analyzing data from various stages of production, automakers can identify potential issues early on and take corrective action before they become more significant problems down the line.
Additionally, this new tool provides greater transparency into the manufacturing process for both automakers and consumers. With real-time updates available at every stage of production, customers can have greater confidence in the end result and trust that they’re getting a high-quality product.
These benefits enable car manufacturers to produce better cars while also saving money and reducing their impact on the environment – making it a win-win situation for everyone involved in car manufacturing.
The potential downside of this new tool
While the new tool for car manufacturing has many benefits, there are also potential downsides that need to be considered. One of these downsides is the possibility of job loss in the industry. With this new technology, fewer workers may be needed on assembly lines and in other areas of production.
Another downside is the cost associated with implementing this tool. While it may ultimately save money in the long run, initially purchasing and installing it can be quite expensive. This could lead to higher prices for consumers or reduced profits for manufacturers.
There is also a concern about over-reliance on technology. If something were to go wrong with the tool or if it became outdated quickly, there could be significant delays and disruptions in production.
There is a risk that this new technology will widen the gap between larger manufacturers who can afford to implement it and smaller ones who cannot. This could lead to further consolidation within the industry and less competition overall.
While this new tool has many potential benefits, its implementation requires careful consideration of all its possible consequences.
Conclusion
The introduction of this new tool is definitely changing the game in car manufacturing. The benefits are undeniable – faster production times, higher accuracy and increased efficiency all lead to lower costs for manufacturers and potentially lower prices for consumers. However, it’s important to keep an eye on potential downsides such as job losses for workers who may be replaced by machines.
We can expect to see more advancements like this one in the future as technology continues to advance rapidly. It’s important for both manufacturers and consumers alike to stay informed about these developments so that they can make the most informed decisions possible when it comes time to buy or produce a car. With all of these exciting changes happening in the industry, it will be interesting to see what other innovations come next!